A Comprehensive Overview to the Process and Benefits of Plastic Extrusion
In the substantial world of manufacturing, plastic extrusion arises as a crucial and very reliable procedure. Transmuting raw plastic right into continuous accounts, it provides to a variety of markets with its exceptional flexibility. This overview intends to elucidate the complex steps associated with this technique, the kinds of plastic suitable for extrusion, and the game-changing advantages it offers the industry. The taking place conversation guarantees to unravel the real-world impacts of this transformative procedure.
Comprehending the Basics of Plastic Extrusion
While it may appear complex at very first glance, the procedure of plastic extrusion is fundamentally simple - plastic extrusion. It is a high-volume production technique in which raw plastic is thawed and shaped into a continual account. The process starts with the feeding of plastic material, in the kind of powders, pellets, or granules, into a warmed barrel. The plastic is after that thawed using a combination of heat and shear, applied by a revolving screw. As soon as the molten plastic gets to the end of the barrel, it is compelled through a little opening called a die, forming it right into a desired form. The shaped plastic is then cooled, solidified, and reduced right into wanted sizes, completing the procedure.
The Technical Process of Plastic Extrusion Explained
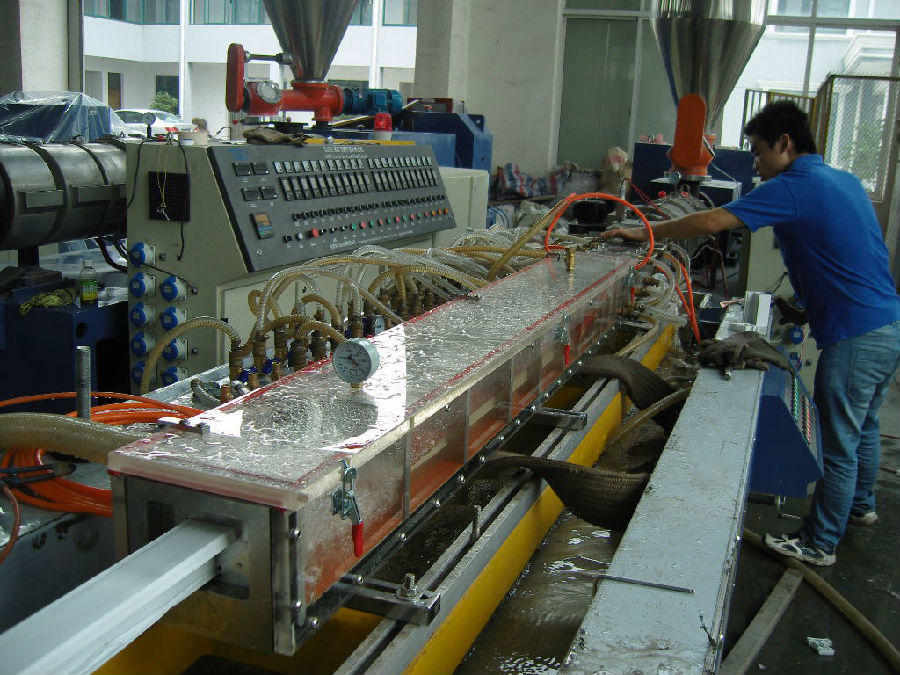
Kinds of Plastic Suitable for Extrusion
The choice of the appropriate type of plastic is an important aspect of the extrusion procedure. Various plastics supply unique residential properties, making them more matched to particular applications. Recognizing these plastic kinds can dramatically improve the extrusion procedure.
Comparing Plastic Extrusion to Other Plastic Forming Approaches
Recognizing the types of plastic ideal for extrusion paves the means for a wider discussion on how plastic extrusion stacks up versus other plastic forming methods. Plastic extrusion is unparalleled when it comes to developing continuous profiles, such as pipes, seals, and gaskets. It also allows for a constant cross-section along the size of the item.
Secret Benefits of Plastic Extrusion in Production
In the realm of manufacturing, plastic extrusion supplies many substantial advantages. One noteworthy advantage is the cost-effectiveness of the process, that makes it a financially appealing manufacturing technique. Furthermore, this technique provides remarkable product adaptability and improved production rate, thereby raising overall production efficiency.
Affordable Production Technique
Plastic extrusion jumps to the forefront as an economical manufacturing technique in manufacturing. Additionally, plastic extrusion needs much less energy than traditional manufacturing techniques, adding to lower operational costs. In general, the financial benefits make plastic extrusion a highly attractive alternative in the manufacturing market.

Superior Product Versatility
Beyond the cost-effectiveness of plastic extrusion, another considerable benefit useful link in making lies in its premium product flexibility. This procedure enables the production of a large selection of items with differing styles, forms, and sizes, from basic plastic sheets to complex accounts. The flexibility is connected to the extrusion die, which can be customized to generate the desired product layout. This makes plastic extrusion an optimal option for markets that call for customized plastic elements, such as auto, building, and product packaging. The pop over to this web-site ability to create diverse items is not just valuable in meeting certain market needs but additionally in making it possible for manufacturers to explore new item lines with minimal resources financial investment. Basically, plastic extrusion's product flexibility cultivates technology while enhancing functional effectiveness.
Boosted Production Rate
A considerable advantage of plastic extrusion hinges on its enhanced manufacturing speed. This manufacturing procedure permits for high-volume production in a fairly short time period. It is capable of generating long, continuous plastic profiles, which considerably decreases the manufacturing time. This high-speed production is especially useful in markets where large quantities of plastic components are needed within tight target dates. Few other manufacturing processes can match the rate of plastic extrusion. Furthermore, the capability to keep constant high-speed manufacturing without compromising product quality establishes plastic extrusion in addition to other techniques. The enhanced manufacturing speed, therefore, not only enables manufacturers to meet high-demand orders but likewise adds to increased efficiency and cost-effectiveness. This helpful attribute of plastic extrusion has made it a favored selection in countless industries.
Real-world Applications and Influences of Plastic Extrusion
In the world of production, the technique of plastic extrusion holds extensive value. This procedure is extensively utilized in the production of a selection of items, such as plastic tubing, additional reading home window structures, and climate stripping. Consequently, it significantly influences markets like construction, product packaging, and vehicle markets. Its effect extends to daily things, from plastic bags to tooth brushes and non reusable cutlery. The economic advantage of plastic extrusion, mainly its cost-effective and high-volume outcome, has transformed production. The environmental effect of plastic waste continues to be a worry. The market is persistently striving for developments in recyclable and eco-friendly products, indicating a future where the advantages of plastic extrusion can be kept without endangering environmental sustainability.
Conclusion
In verdict, plastic extrusion is a extremely effective and efficient approach of transforming raw materials into diverse products. It uses many benefits over other plastic forming techniques, including cost-effectiveness, high output, very little waste, and design versatility. Its impact is greatly felt in numerous sectors such as construction, automotive, and durable goods, making it a critical procedure in today's production landscape.
Digging much deeper into the technical process of plastic extrusion, it starts with the choice of the appropriate plastic material. As soon as cooled down, the plastic is reduced right into the needed lengths or injury onto reels if the item is a plastic film or sheet - plastic extrusion. Comparing Plastic Extrusion to Various Other Plastic Forming Approaches
Comprehending the types of plastic ideal for extrusion paves the method for a more comprehensive conversation on just how plastic extrusion piles up against various other plastic creating methods. Few various other production processes can match the rate of plastic extrusion.